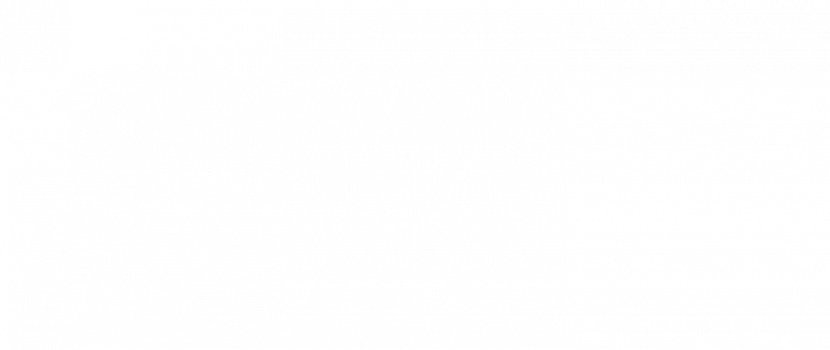
Which Plating Option is Best for My Composite Connector?
Different connectors have different uses based on the substrate and plating material. Substrate selection for the base material of a composite connector is crucial in aerospace and defense, and other uses because of its role in determining the connector’s performance and reliability. The substrate material must be able to withstand the harsh conditions, including high and low temperatures, lightning strikes, and exposure to various types of corrosion. Beyond substrate, surface preparation, plating material, and plating methodology will all contribute to the types of potential uses for the connector. Plating onto substrates such as PEEK and Ultem with copper, nickel, and tin-based metals can all determine the effective end-use of different connectors.
Surface Activation®
Surface Activation® is a proprietary process used to improve the adhesion of the metal plating to a composite substrate. It is particularly useful for high-performance materials like PEEK and Ultem, which are used extensively in aerospace and military products. Surface Activation® does not damage the surface or degrade critical geometries of a component. Unlike media blasting or aggressive etching, Surface Activation® is a highly controlled and repeatable process that can be used for high-volume production plating, as well as low-volume R&D.
PEEK (polyetheretherketone) is a thermoplastic material that is known for its excellent mechanical and chemical resistance, high strength and stiffness, and low coefficient of thermal expansion. PEEK is also biocompatible, making it an ideal material for medical applications. However, PEEK is also known to have a low surface energy, which makes it difficult to bond to other materials. Surface Activation® is an excellent solution used to plate PEEK.
Similarly, Ultem (polyetherimide) is another high-performance thermoplastic with outstanding mechanical and thermal properties, high strength and stiffness, and low moisture absorption. Ultem is also biocompatible and can be sterilized, making it perfect for medical applications. Ultem also shares the same issue with PEEK, that is, it has a low surface energy which makes it difficult to plate and bond to other materials.
There are legacy surface preparation methods that can be used to promote the plating adhesion on connectors, such as chemical etching and mechanical abrasion.
Chemical etching involves using a chemical treatment to create a more porous surface on the connector, which allows for better adhesion to the substrate. Common chemical treatments include chromic acid, permanganate, hydrofluoric acid, and others. Most of these are highly toxic and have special handling requirements. Mechanical activation, on the other hand, uses a mechanical method to create a more porous surface on the connector, such as sandblasting or bead blasting. It is possible to find success with these etching methods, but platers generally will experience quality control and plating adhesion challenges in a production setting.
PEEK and Ultem
PEEK (polyetheretherketone) and Ultem (polyetherimide) are high-performance thermoplastics that are commonly used in aerospace and defense, medical, and other extreme environments. Both materials have excellent mechanical and thermal properties, high strength and stiffness, and low moisture absorption. However, due to their low surface energy, PEEK and Ultem can be challenging to plate.
PEEK and Ultem plating methodologies are typically divided into two categories: electroless plating and electroplating.
Electroless plating: This method is a chemical process that does not require an external power source to deposit metal onto the surface of the PEEK or Ultem connector. The metal ions are reduced to metal by a chemical reducing agent, and the metal deposit is formed. Electroless plating can be used to deposit a variety of metals, including copper, nickel, gold, and palladium. Electroless plating is typically more uniform than electroplating, and it can be used to plate complex shapes.
Electroplating: This is a widely used method where a metal layer is deposited on the surface of the connector by way of electrochemical deposition. This involves the use of an anode (desired metal plating) to be transferred onto the cathode (product to be plated) in the plating bath with the use of direct current.
The ideal use case for PEEK and Ultem plating will depend on the specific requirements of the application and the environment in which the connector will be used. For example, if the connector will be used in an environment that experiences intense thermal cycling, copper and nickel plating may be the best choice. If the connector will be used in a highly corrosive environment, plating with a high-phosphorus nickel will be the best option.
Customers may want to choose PEEK or Ultem substrates for their connectors because of the excellent mechanical and thermal stability of the materials. PEEK and Ultem are also highly resistant to chemicals and have low moisture absorption, making them ideal for use in aerospace, military, medical, and electronic industries.
It is important to note that in order to maximize the performance of PEEK and Ultem connectors, it is critical that the surface preparation be done correctly and that the plating process is carried out by a reputable and experienced shop. Plating adhesion is often the most critical aspect to plating PEEK and Ultem. Adequate adhesion must be achieved to ensure that the connector performs reliably and safely in the demanding environments in which it will be used.
Other Plating Options
There are several plating options available for connectors in addition to the commonly used nickel and tin plating. Each option has its own set of advantages and disadvantages, and the choice of plating will depend on the specific requirements of the environment in which the connector will be used.
Mid-phosphorus Electroless Nickel
Mid-phosphorus nickel is a type of nickel plating that is used for corrosion resistance, hardness, wear resistance, and good solderability. It is often used in connectors for aerospace, automotive, and electronic applications. The hardness is typically 45 to 57 Rc.
High-phosphorus Electroless Nickel
High-phosphorus nickel is a type of nickel plating known for its excellent corrosion resistance. This type of plating is often applied to connectors used in the aerospace and automotive industries.
Boron Nickel
This is another type of nickel plating with superb corrosion resistance and hardness. This type of plating has excellent surface hardness, averaging 65-70 C on the Rockwell scale.
Teflon Nickel
Teflon nickel plating has great properties for corrosion resistance, wear resistance, and lubricity. It is most frequently applied to connectors for aerospace and electronic applications.
Lead or Lead-Free Tin
This is a type of tin plating that is known for its solderability and good corrosion resistance. Lead-free tin is becoming increasingly popular due to concerns about lead toxicity.
Copper Plating
Copper plating is often used in connector applications to enhance the EMI shielding characteristics. However, copper does not have adequate corrosion resistance and needs a top layer of nickel in order to ensure the plated product can survive in its intended environment.
It’s worth mentioning that in addition to the plating options, there are other surface treatments that can be used on connectors. For example, passivation is a process used to improve the corrosion resistance of metallic connector surfaces by removing contaminants and creating a protective oxide layer on the surface. Anodizing is a process of electrochemically increasing the thickness of the natural oxide layer on the surface of metal parts, which increases the corrosion resistance of the surface and improves the aesthetic appearance.
The Use Determines the Plating
The use of the connector will ultimately determine the type of plating needed. Different types of plating provide different levels of protection, performance, and functionality in different environments and conditions. For example, if a connector is going to be used in a high-temperature aerospace and defense environment, a plating that can withstand high temperatures, such as nickel, would be required. If the connector is going to be used in a corrosive environment, a plating that is highly resistant to corrosion, such as high-phosphorus nickel or gold, would be needed. A connector used in medical applications may require a plating that is biocompatible and can be sterilized, such as gold.
Conclusion
The use of a connector will help determine what sort of plating is the best option. Before choosing a plating option, it’s best to consult with a plating specialist to ensure your connector is properly protected. SAT Plating specializes in plating high-performance plastics and works with a variety of industries, including aerospace, defense, medical, and industrial markets. Please contact us if you have any questions regarding the best plating service for your organization.