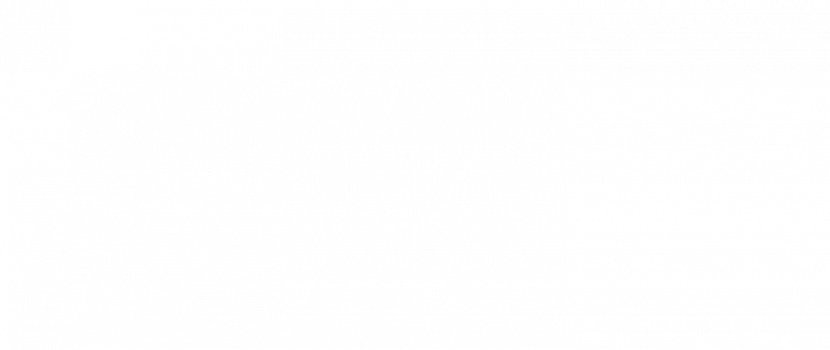
Plating Injection Molded Composite Connectors for Aerospace Engineers
There are thousands of connectors on airplanes, defense systems, and vehicles. The high performance and highly technical interfaces utilized in these electronic systems require durability, corrosion resistance, and production consistency. These specifications make the concept of using injection molded and plated connectors a smart choice for any advanced wiring system.
More specifically, injection molding with innovative polymers like PEEK and Ultem (PEI) offers enhanced functionality and performance while accommodating the market’s demand for the cost savings that light-weighting products can provide. Plating these parts with metals adds desirable qualities such as EMI shielding and corrosion protection.
Why Use Plated Injection Molded Parts for Aerospace Products?
The aerospace systems of tomorrow will be stronger, lighter, and more agile than ever before. Engineers are taking advantage of advancements in science that have led to materials that perform with higher strength at lower weight. Injection molding these engineered polymers helps manufacturers achieve increasing efficiencies, economies of scale, and meet strict performance requirements.
Polymers with greater thermal stability and higher strength-to-weight ratios must also be able to operate in increasingly demanding environments and possess the qualities to meet exacting technical specifications. Even the smallest discrepancy in measurements, weight, or materials can make the connector ineffective and a risk to the overall product.
Aerospace industry designers are particularly interested in plating injection molded plastic connectors to add EMI shielding and electrical grounding properties. Plating connector housings with copper and nickel protects the power and data flowing through a complex system.
Plating Injection Molded Connectors
Plating on high-performance plastics can present specific challenges, though selecting the right plating partner can result in connectors with the exact qualities aerospace design engineers need to meet today’s tight performance standards. Plated polymer connectors are lighter than the same components made from machined aluminum or stainless steel. Plus, using plated PEEK or Ultem connectors in a wiring system can result in significant overall weight savings.
While some design teams still prefer stainless steel or aluminum for their connector shells, there are many compelling reasons to move to plated PEEK or Ultem, including their proven ability to perform during extreme temperature cycling, corrosion testing, and vibration and mating cycle testing.
Selecting a Plating Partner for Plated Injection Molded Connectors
When developing a connector using PEEK or Ultem with metal plating, there are several aspects to consider, beyond the exacting standards and quality control measures. When selecting a plating partner, ask these questions:
- Do they have a history of meeting extreme environment testing requirements?
- At the outset of a new program, will they help you develop a Design of Experiment (DOE) to explore all design and engineering possibilities?
- Does the company have a demonstrated track record in the aerospace, defense, or other high-precision industries?
- Will they collaborate with your engineering team at the beginning and end of the process to ensure objectives are met?
A plating partner should have a solid knowledge base about injection molded parts, in order to be able to solve any potential issues before they arise during the development and testing phase of development. Adjustments to design, material and plating thicknesses can make a world of difference to the end result when plating polymers with precise and critical performance specifications.
Precise Plating for Injection Molded Polymer Parts
At SAT Plating, our team has a solid understanding of the injection molding process and, more specifically, how metal plating works with injection molded high-performance polymers. Consider us a collaborative partner from Phase Zero to approved production for new programs. We also help organizations upgrade products from aluminum or stainless steel to a plated composite. We are specialists in plating PEEK and Ultem components with various metal finishes and able to meet tight specifications, even for programs with 1,000 to 1,000,000 parts per year. Let’s talk plating on polymers.