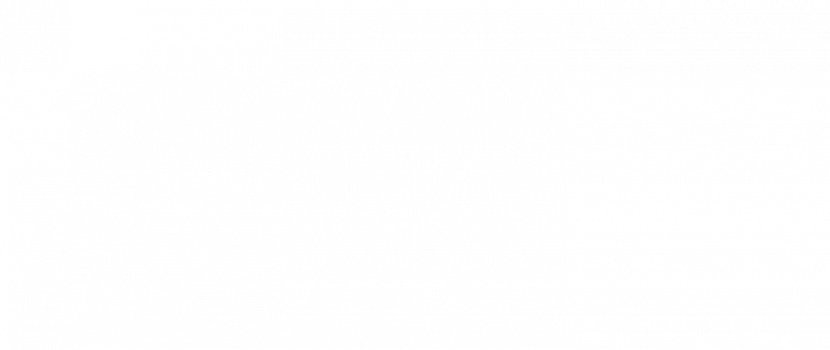
The Evolution of the U.S. Defense Industrial Base & Surface Finishing
The U.S. defense industrial base is the network of companies, research institutions, and other organizations that produce goods and services for the U.S. military. It is a critical component of the U.S. national security apparatus, providing the military with the equipment, technology, and other resources it needs to defend the country. Surface finishing is a process that modifies the surface properties of a material, such as its conductivity, corrosion resistance, and wear resistance. It is an important aspect of the defense industry, as many military systems and equipment require specialized surface finishes to meet the demanding requirements of their intended use. Surface finishing techniques are used to protect and enhance the performance of military aircraft, ships, vehicles, weapons, and other systems.
Early History of the Defense Industrial Base
The defense industrial base has its roots in World War II, when the U.S. government mobilized its industrial capacity to support the war effort. The government established the Office of Production Management to coordinate the production of military goods, and implemented measures such as price controls and rationing to ensure that the necessary resources were available to support the war. After the war, the defense industrial base underwent a significant expansion during the Cold War, as the U.S. sought to counter the military threat posed by the Soviet Union. The government established a number of programs, such as the Defense Production Act and the National Defense Education Act, to stimulate the production of military goods and to invest in research and development. The defense industrial base also expanded through the growth of large defense contractors, which played a key role in supplying the military with advanced technology and equipment.
Modernization of the Defense Industrial Base
Following the end of the Cold War, the U.S. defense industrial base began to change and shrink as the military’s priorities and budgets shifted. The defense budget declined, leading to a reduction in the number of large defense contracts and an increased focus on cost-cutting measures. At the same time, the defense industry faced increased competition from foreign manufacturers, as globalization led to the expansion of international trade and the movement of production to lower-cost countries.
To adapt to these changes, the defense industrial base underwent a process of restructuring and consolidation, as companies merged or went out of business. At the same time, the defense supply chain saw the emergence of small and medium-sized enterprises (SMEs), which played an increasingly central role in supplying the military with goods and services. These companies often specialize in niche markets or offer unique technologies, and they have the agility to respond quickly to changes in demand. The inclusion of SMEs in the defense supply chain has helped to increase competition and innovation within the industry.
The Role of Surface Finishing in the Defense Industry
Surface finishing on plastics and other components is an important aspect of the defense industry. Many military systems and equipment use plastic components that require specialized surface finishes to meet the demanding requirements of their intended use. There are several types of surface finishing techniques that can be used on plastics, including plating, anodizing, vapor deposition, and others which can be used for a number of different ends.
EMI Shielding
Electromagnetic shielding with surface plating is important in the aerospace and defense industry because it helps to prevent interference with electronic systems on aircraft and defense equipment. This is achieved by applying a conductive layer to the surface of the component, which helps to block or absorb electromagnetic radiation. Surface plating can be an effective method for achieving electromagnetic shielding, as it can be applied to a wide range of materials and can be easily integrated into the manufacturing process.
Lightweighting
“Lightweighting” is important because it helps to reduce the weight of components and equipment, which can lead to improved performance and fuel efficiency. This can be particularly important in the aerospace industry, where reducing weight can help to increase the range and payload capacity of aircraft, as well as reduce operating costs.
Wear Resistance
Wear-resistant plating helps to extend the lifespan of high-use components, such as landing gears and engine parts. These components are subject to constant wear and tear, and wear-resistant plating can help to protect them from the effects of friction and abrasion, improving their performance and reducing maintenance and repair costs. Wear-resistant plating can also help to improve the overall performance of the aircraft or equipment by ensuring that these critical components are able to function reliably over time.
Corrosion Resistance
Corrosion resistant plating is essential to protect components from damage caused by exposure to the elements, such as moisture and salt. This is particularly important for aircraft and defense equipment that are operated in harsh environments, as corrosion can weaken structural components and reduce their performance and lifespan. Corrosion resistant plating can help to extend the lifespan of components and improve the overall performance and reliability of the aircraft or equipment.
Lightning Strike Protection
Lightning strike surface finishing is one of the most important uses for surface finishing in A&D. It protects aircraft and defense equipment from damage caused by lightning strikes which would otherwise cause significant damage to the structural and electronic systems on aircraft. Lightning strike surface finishing can help to dissipate the energy of the strike and reduce the risk of damage, keeping passengers and the crew safe in dangerous situations. This is particularly important for aircraft that operate in areas with a high risk of lightning strikes, as it can help to ensure the safety and reliability of the aircraft.
Added Lubricity
Added lubricity reduces friction and wear on components, improving their performance and lifespan. This is particularly important for high-use components that are subject to constant friction and abrasion, such as gears and bearings, as it can help to extend their lifespan and reduce maintenance and repair costs. Added lubricity surface finishing can also help to improve the overall performance and reliability of aircraft and defense equipment by ensuring that these components are able to function smoothly and reliably over time.
With the current state of manufacturing in America, all of these practices along with tens-of-thousands of others in the A&D industry are at risk. In the event of a hot conflict with another country, the manufacturing and throughput capacity is currently inadequate to meet the demands of defense efforts. It’s imperative that A&D OEMs, primes, and anyone in the supply chain work with governments to develop a plan and readiness strategy in the event that a production increase is needed.
Challenges and Opportunities for the Defense Industrial Base
Manufacturing plated aerospace and defense components can be impacted by environmental regulations, which can require manufacturers to implement costly pollution control measures and impose limits on the use of certain chemicals. Non-compliance with these regulations can result in fines and damage to a company’s reputation. These regulations also pose a potential national security threat to the US as they may limit the production of lightweight conductive pieces necessary for maintaining low aircraft weight and may increase the country’s dependence on foreign manufacturing, potentially resulting in a loss of American jobs.
Conclusion
In conclusion, the U.S. defense industrial base has undergone significant evolution over the past century, from its origins in World War II to its expansion during the Cold War and its modernization in the post-Cold War era. Surface finishing is an important aspect of the defense industry, as it enhances the performance and durability of military systems and equipment through techniques such as plating, anodizing, and vapor deposition etc. Environmental regulations pose a significant challenge for the manufacturing of plated aerospace and defense components, but there are also opportunities for the defense industrial base to capitalize on advances in advanced manufacturing technologies and the inclusion of small and medium-sized enterprises in the defense supply chain. Despite the challenges and changes it has faced, the defense industrial base remains a vital component of U.S. national security, providing the military with the resources it needs to protect the country.
SAT Plating specializes in plating high-performance plastics and works with a variety of industries, including aerospace, defense, medical, and industrial markets. Please contact us if you have any questions regarding the best plating service for your organization.