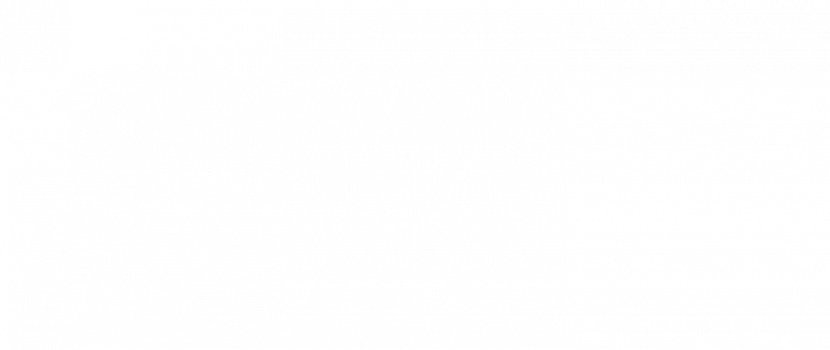
Advancements In Industrial Electroplating on PEEK and Ultem
Technology advancements in industrial electroplating have been a direct result of developing and increasing use of PEEK, Ultem, and other high-performance polymers in manufacturing.
Tech Advancements Lead Industrial Electroplating Innovation
As technology races forward, industrial designers and engineers are constantly looking for polymer materials with greater thermal stability and higher strength-to-weight ratios that can operate in increasingly demanding environments.
Aerospace, defense, automotive, and medical industries are particularly interested in plating for EMI and RFI shielding. Transitioning from machining a component out of aluminum to injection molding using polymer plastics helps manufacturers achieve efficiencies and economies of scale.
When engineers need characteristics associated with metal on these molded parts, specifically corrosion resistance or electromagnetic shielding, industrial electroplating can innovate to meet that need.
The Future Brings Smaller, Lighter Components
Aircraft and vehicle components are getting smaller and lighter, with electronics being encased into tight spaces while being forced to meet even more demanding performance requirements.
In one example, automotive manufacturers are rapidly creating new and exciting options for future mobility, self-driving, and electric vehicles. With GPS, RADAR, LiDAR, and RF systems, vehicles will essentially become transmitters and receivers, with the inevitable accompanying signal interference issues. OEMs have, as a result, become more appreciative of the incredible value of shielding.
As the automotive industry continues to develop electric vehicles, there is sure to be even more significant change over the next few decades. EVs and their engines have a much smaller number of components, with simpler systems than a traditional internal combustion engine. The changeover to EVs is sure to bring about many opportunities for plating suppliers who choose to follow the innovation.
Plating on plastics like PEEK and Ultem will require leveraging the benefits of these plastics and optimizing the plating process to pass the increasingly stringent requirements of the aerospace, defense, automotive, and medical industries.
Industrial Electroplating on Polymers and Composites
SAT Plating’s Surface Activation®️ process was initially developed to allow optimal plating on composites and interconnect housings. It allows SAT Plating technicians to permanently and fundamentally change the surface of the polymer, with no erosion of the surface and no potential contaminants. Surface Activation®️ is performed in a controlled environment and allows the plating chemicals to achieve outstanding adhesion. Of course, surface preparation is critical to the success of the process.
While many industrial electroplating operations can do small volume Ultem and PEEK jobs, using media blasting, vibratory etching, or other processes, it’s often not scalable, affordable, or efficient. It’s wasteful and results in a high volume of scrap.
Industrial Electroplating Quality Standards for the Future
Both aerospace and automotive manufacturers hold high-quality standards for industrial electroplating on polymers, and their requirements can be intricate. For example, some PEEK or Ultem components may only need plating on a specific limited area. Any deviation can be detrimental to the success of the project. Plating companies that can deliver on detailed targets at the customers’ desired price point will succeed now and into the future.