Unshackle Your Material Choices: Satellite & Microwave Systems
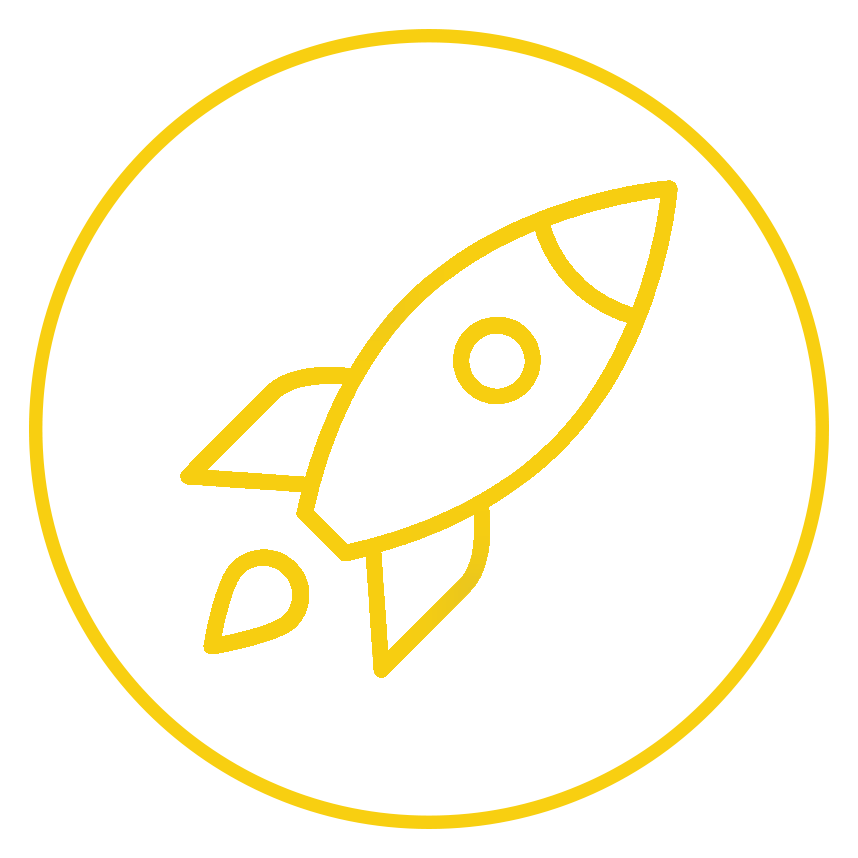
Government agencies and private companies like SpaceX — Lockheed Martin — OneWeb — and others — are making space and communication systems more accessible than ever. These entities are deploying satellite and ground microwave systems at an exponentially accelerating rate.
A common denominator for all these enterprises is finding lighter-weight; higher-performing materials that can reduce costs, improve efficiency and maintain operating requirements over legacy machined metal components. That translates into plastics.
SAT Plating is continuously engaged in satellite and microwave component development with numerous manufacturers of aerospace, satellite and defense systems. As these technologies race forward — the designers and engineers we work with — are constantly looking for polymer materials that have greater thermal-stability and higher strength-to-weight ratios that can operate in demanding environments.
That means polymers like Ultem – PEEK – Carbon Fiber – and all manner of glass-filled & composite materials are being tested – approved – and used as metal replacements.
Heretofore, many engineers considered these high-performance, thermally-stable composite plastics to be “unplateable” because traditional plating methods could not ensure consistent, reliable plating performance. For satellites and other “mission critical” components, plating adhesion is an absolute requirement. That’s why SAT Plating’s proprietary Surface Activation® process is a breakthrough technology.
Our gas-phase treatment dramatically & permanently increases the surface energy of the polymer – increasing plating adhesion at an atomic level. There is no change in the physical shape or basic characteristics of the treated plastics or components. This treatment enables high-adhesion of metal platings without eroding the surface – or damaging fine details of the component – as with blasting or chemical etching. An added plus… Surface Activation® is a completely green process — with zero environmental impact.
In concert with our proprietary Surface Activation® Processing – our in-house custom masking solutions add multi-functional integration on components that can further reduce weight and optimize costs. We can attain myriad functional and performance features such as: antennas – conductivity – EMI shielding – UV protection – the ability to withstand intense radiation – and other characteristics like superior adhesive bonding.
One of the greatest values we bring to a client’s project is when we are consulted during the proof-of-concept period – when engineers and designers are selecting a polymer to meet product design goals.
SAT Plating is ITAR Registered & Compliant as well as ISO 9001:2015 Certified.