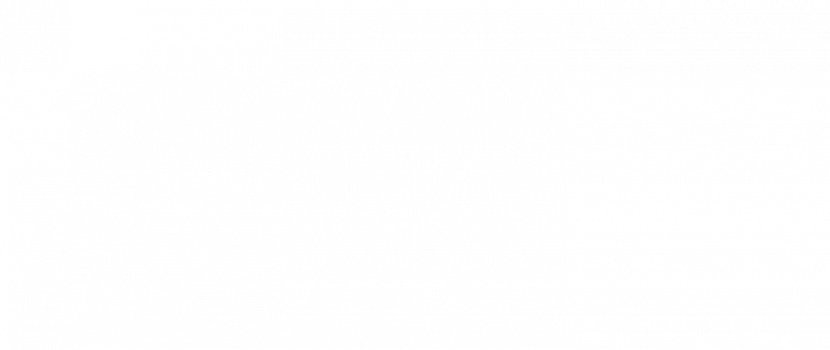
Fly Lighter, Fly Farther: Plating Plastics for Aerospace
Making aircraft parts lighter is one of the easiest ways to improve the effective range of the aircraft; the less weight a turbine must move, the farther it can go. At the forefront of this race for lightweighting lies the integration of plated plastics and composite materials into aircraft components. This transformative advancement of aviation technology is set to propel the industry to unprecedented heights and at unprecedented speeds. By significantly reducing fuel consumption, operational costs, and the carbon footprint, these groundbreaking materials stand as formidable challengers to the conventional use of aluminum or stainless steel components in the aerospace industry, ushering in an era where aircraft can indeed fly lighter and fly farther.
The Rising Trend of Plating Plastics in Aerospace
The rising trend of plating plastics in aerospace signifies a remarkable evolution in aircraft manufacturing technology. This innovative approach involves the application of metallic coatings onto plastic components, contributing to the development of lighter, more efficient aircraft. The growing adoption of plating plastics in aerospace can be attributed to significant advancements in materials science, particularly the development of high-strength, high-quality plastics and polymers.
Historically, the aerospace industry faced challenges when it came to incorporating plastics due to their inherent limitations in terms of strength and durability. However, recent technological breakthroughs have addressed these shortcomings, enabling the use of plated plastics in critical aircraft components such as connectors and EMI-shielded housings. These breakthroughs include the development of advanced composite materials, enhanced plating techniques, and rigorous quality control measures. As a result, plated plastics have emerged as a viable and advantageous option in aerospace manufacturing, offering reduced weight, improved fuel efficiency, and enhanced aircraft agility.
Fuel Efficiency and Carbon Savings
The adoption of plastics in aircraft manufacturing, particularly plated plastics and composite materials, brings substantial fuel efficiency gains and carbon savings to the aerospace industry. One of the primary advantages of utilizing these lightweight materials is the significant reduction in aircraft weight. Lighter aircraft consume less fuel, leading to tangible cost savings for airlines and operators, as well as a notable decrease in carbon emissions. This weight reduction translates into enhanced fuel efficiency, allowing aircraft to cover longer distances on the same amount of fuel.
Moreover, the environmental benefits are considerable; reducing fuel consumption results in a smaller carbon footprint. In an era marked by global environmental concerns, the alignment of these carbon emissions reductions with international environmental goals underscores the pivotal role that the aerospace industry plays in addressing climate change. By embracing lightweight materials like plated plastics, the industry not only improves its economic efficiency but also contributes to a more sustainable and environmentally responsible future.
Operational Cost Reduction
The integration of plated plastics in aircraft components offers a substantial advantage in terms of operational cost reduction. When compared to traditional materials like aluminum or steel, plated plastics exhibit remarkable cost efficiencies throughout their lifecycle. The manufacturing of plastic components is notably cost-effective, thanks to streamlined production processes and the ease of molding and 3D-printing intricate shapes. These advantages translate into reduced production costs and quicker turnaround times.
Plated plastics are also inherently corrosion-resistant, eliminating the need for frequent maintenance and costly repairs associated with corrosion-prone metals frequently used on aircraft. As a result, operators benefit from extended maintenance intervals, reduced downtime, and lower maintenance costs. The cost-effectiveness and speed of production afforded by plated plastics contribute significantly to the overall cost-efficiency of aircraft manufacturing and operation, making them an increasingly attractive choice.
Enhanced Performance and Durability
Plated plastics offer an exceptional balance of strength, durability, and reduced weight, enhancing overall aircraft performance and longevity. In particular, the use of heat-resistant and noncorrosive plastics to replace traditional metal fasteners and screws has proven instrumental in improving the durability of critical aerospace components. Plastics with high-temperature resistance properties enable these components to withstand the extreme conditions of flight, including exposure to intense heat and rapid temperature fluctuations.
For example, in engine components and interior cabin structures, plated plastics have demonstrated their ability to perform comparably to metal counterparts. These plastics not only maintain their structural integrity under demanding conditions but also contribute to reduced weight, which is vital for optimizing fuel efficiency and operational performance. As a result, the aerospace industry increasingly relies on plated plastics to achieve superior durability and enhanced overall performance in various critical aircraft components.
Conclusion
The incorporation of plated plastics and composite materials in aerospace manufacturing is not merely a fleeting trend, but a substantial leap toward achieving fuel efficiency, cost reduction, and environmental sustainability. By progressively replacing metal components wherever possible, the aerospace sector is better positioned to meet the rigorous demands of modern-day aviation while contributing positively to global carbon reduction efforts. Selecting the right plating material and designing the component correctly must be done with the help of experienced professionals like SAT Plating. SAT Plating offers comprehensive support to companies, spanning the entire spectrum from research and development to large-scale manufacturing and seamless product delivery. Contact our knowledgeable team today to initiate a conversation about your project’s specific needs and discover how SAT Plating can assist in meeting your exact specifications. Our capabilities extend to accommodating programs that require as few as 1,000 parts or exceed 1 million parts annually.