Plating Nylon
SAT can plate both natural and glass filled nylons
Traditionally, Nylon has not been suitable for plating. The polyamide readily absorbs water, and it is dimensionally unstable in demanding environments. However, at SAT Plating, our Surface Activation® technology allows us to plate the “unplateable”.
Our Adaptive Plating Technologies ensures:
- Improved Wear / Corrosion Resistance
- Scaleable Production
- EMI Shielding
- Cosmetic Enhancement
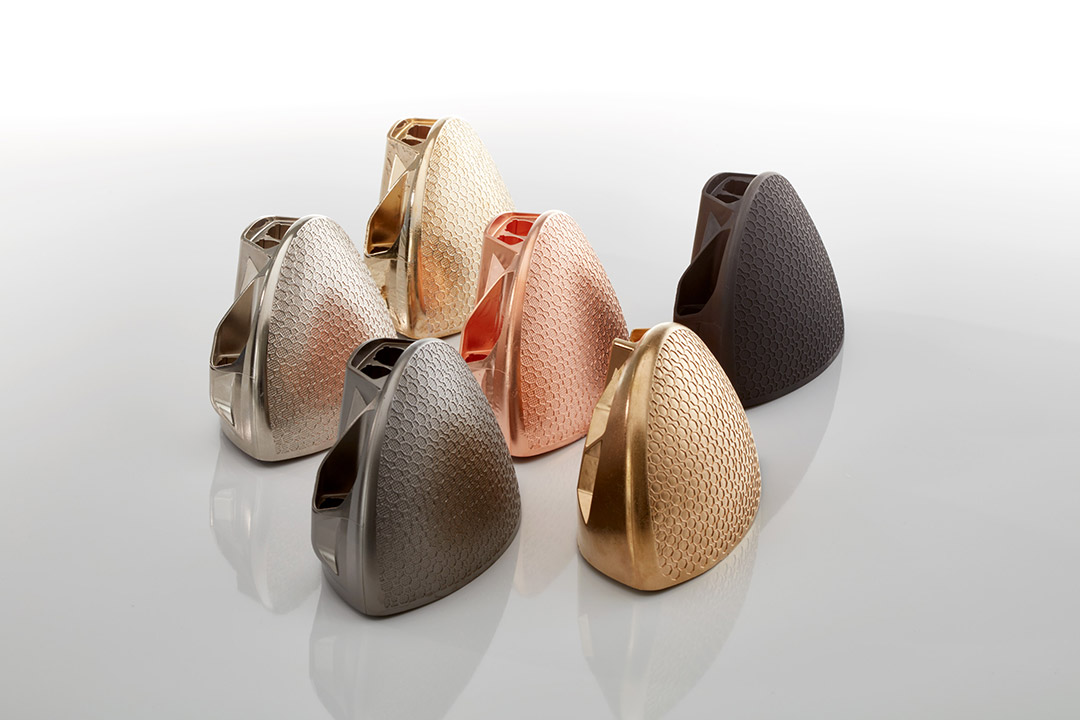
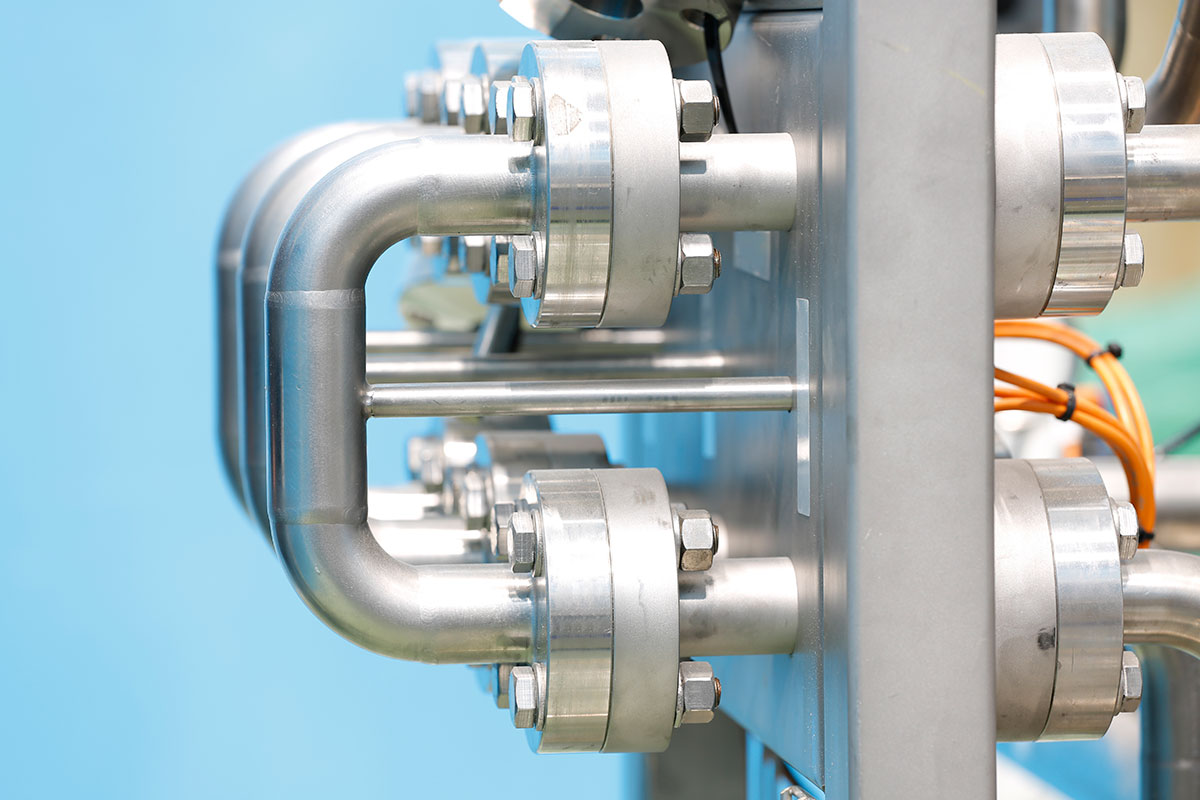
Nylon’s ability to change properties and its function as a composite material also allows it to function for a plethora of applications.
Why Use Nylon?
The malleability of Nylon and its ability to be shaped or injection molded allows it to be very dynamic in its application. This is backed by its increased use in 3D printing and injection molding. This molding potential is also bolstered by its ability to be combined with other materials such as carbon fiber, and glass. These additives are commonly used to meet specific product requirements.
Nylon is a strong yet economical polymer. Now SAT makes it even more versatile with function and aesthetic platings Even though it has low flammability when exposed to open flames, its composite capability affords it the option to combine with flame retardant material, which allows it to be used on car engines and other various high-stress scenarios.
A Closer Look at Nylon
Nylon is a synthetic polymer with a thermoplastic material. Its thermoplastic properties make it extremely pliable. Said pliability affords it the potential to be melted into a plethora of materials including fibers, shapes, or even film. Nylon’s pliable nature has led to it becoming a popular material for 3D printing and other forms of additive manufacturing since it can be easily melted into filaments. It is also a popular material for injection molding because of its malleable properties and its ability to be reinforced with other materials.
Nylon is also commonly used as the matrix material in composite materials due to its ease of bonding. This helps change the composition of the material while also granting it a dynamic quality in regard to its properties through the reinforcement of other materials. It is regularly reinforced with glass or carbon fiber to increase Nylon’s density, its structural and impact strength, its rigidity, and its lubricity. This is done to increase the heat resistance of Nylon, affording it the ability to replace low to medium stress components—especially found within engines—that were generally cast in metal.
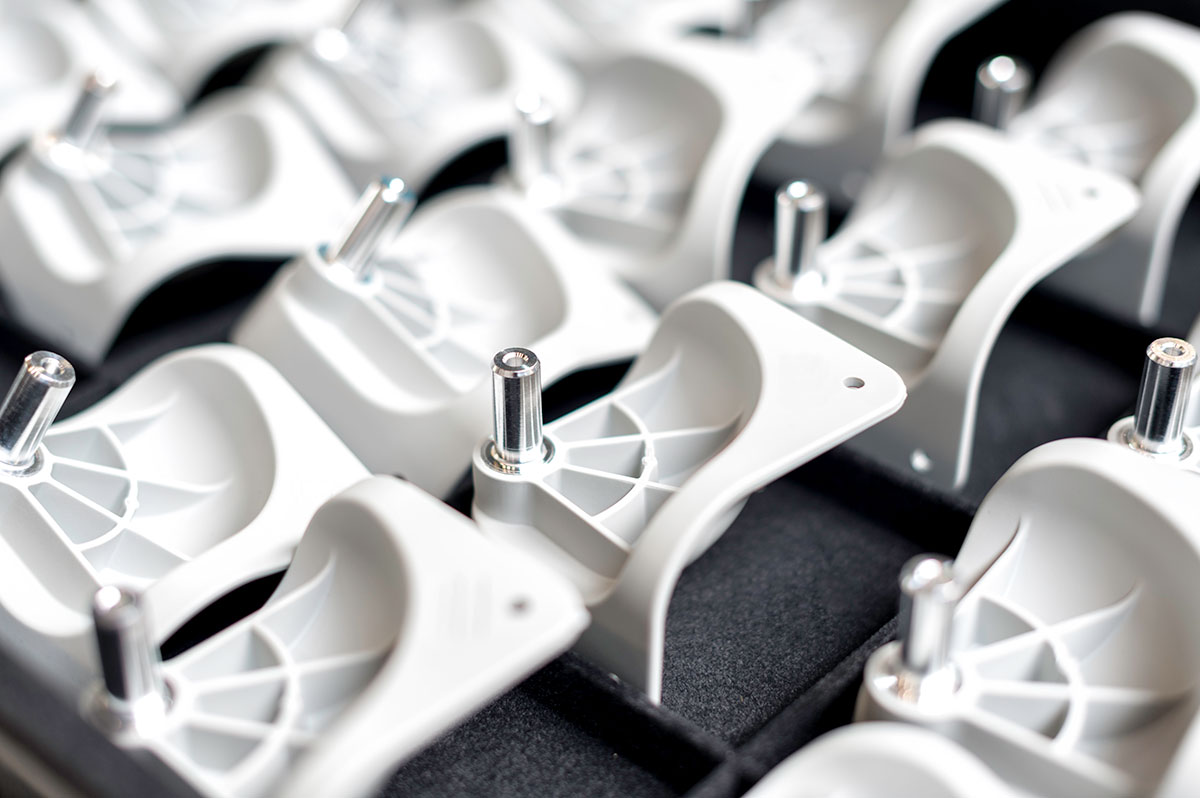
Nylon has a natural melting point and can be reinforced with a flame retardant material to increase its flammability. The melting point of Nylon 6—which is formed with ring-opening polymerization—is 428 °F and Nylon 66—which is formed with amides—is 509 °F. While Nylon is highly flammable, its’ high melting point gives the material flexibility in its application due to its malleable nature.
Nylon is also a strong and long lasting material due to its resistance to multiple factors. It is fairly resistant to moisture absorption and various forms of abrasion, as well as being resistant to a wide array of chemicals. This offers the material the ability to replace a plethora of low strength materials, which is only bolstered by its chemical compatibility.