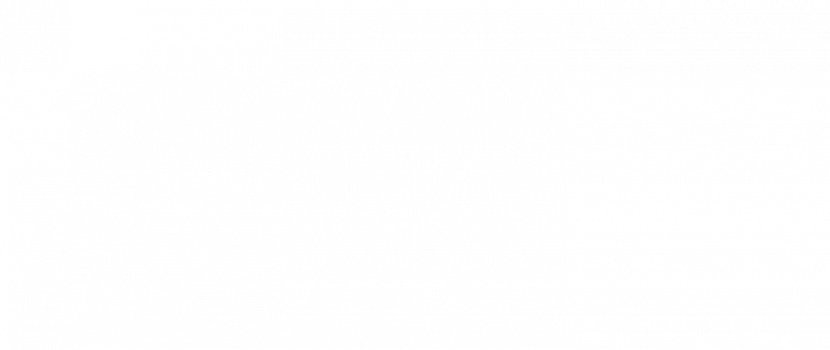
Omnetics Whitepaper for Reliable Connectors on LEO Satellites
Recently, SAT Plating was honored to appear in an Omnetics white paper discussing reliable connectors on LEO satellites. The white paper discussed the necessity of greater resilience for materials used in the manufacturing of LEO satellites. Connectors are a key part of LEOS to aid in radiation protection, EMI shielding, and temperature resistance and must be adequately protected to ensure proper functioning.
Low Earth Orbit Satellites
Low Earth Orbit Satellites are responsible for a significant majority of the communication infrastructure that the world relies upon. These marvels of modern engineering are the result of macro advances in physics, chemistry, and other technologies. Nearly every developed country in the world uses these satellites for surveying, communicating, and defense because of the high quality images and connectivity.
Low Earth Orbit Satellites are also preferable to Medium Earth Orbit Satellites because of their cost. It is substantially easier and more cost-effective to deliver and maintain payload to LEO altitudes. Because of this, LEO delivery is relatively accessible and the demand for both private and governmental LEO infrastructure is likely to continue well into the future.
Challenges with LEOS
LEOS often exist in exceptionally hostile conditions anywhere from 250 – 1200 miles above the earth’s surface. The total lack of atmosphere at these altitudes creates temperatures that range from well below freezing to well above the boiling point of water at sea level. These temperatures are constantly cycling as the satellites pass into, and out of the range of the sun’s heat. This cycling of heat and cold causes expansion and contraction within the entire satellite which can wear out joints, solders, and housings. Given that this cycling occurs several thousand times per year on a satellite, this wear can eventually lead to the total failure of the LEO satellite, should fissures occur.
Additionally, the radiation from the sun is unmitigated by any terrestrial atmosphere, creating an environment that can easily damage circuitry and microprocessors. Alpha, beta, and gamma radiation from the sun represent risks for LEO satellites, many of which have degraded since their initial delivery to LEO. Studies of the efficacy of components in high-radiation environments is currently teaching us more about the best ways to protect against LEO radiation. One such option is plating PEEK composites.
SAT’s Contribution – PEEK Plating and Surface Activation®
SAT Plating is proud to be contributing to the effectiveness and longevity of LEO satellites with an advanced method of plating metals onto PEEK composites used for connectors. To do this, SAT uses its proprietary process called Surface Activation®. Plating PEEK and similar composites is crucial for LEO durability given its radiation-proof properties. Additionally, SAT’s Surface Activation® allows for this type of plating on several materials used in satellites and other industries like Aerospace & Defense, medical, and industrial manufacturing.
Surface Activation® allows PEEK to be plated in several forms, such as films, 3D prints, filaments, and injection molded parts. This process also allows for the material being plated to remain “as-molded” without any modifications to the object’s dimensions. Most importantly for LEO applications, PEEK is a very lightweight thermoplastic. When every ounce at liftoff counts, PEEK reduces mass and allows more payload and more efficient use of fuel, space, and other resources on the rocket.
If you’re currently considering plating PEEK or another composite material, it’s best to consult with an expert to ensure your components are properly handled. SAT Plating specializes in plating high-performance plastics and works with a variety of industries, including aerospace, defense, medical, and industrial markets. Please contact us if you have any questions regarding the best plating service for your organization.