Plating PVC and CPVC
Always considered unplateable, SAT makes chemical resistant and flame retardant PVC and CPV more versatile.
Our Surface Activation® technology allows us to metalize PVC and CPVC with outstanding adhesion, no matter how thin or thick your plating specifications require.
With our Advanced Plating Technologies, we can give you the conductive surface you need for RFI/EMI shielding or multiple bright finishes for aesthetic purposes.

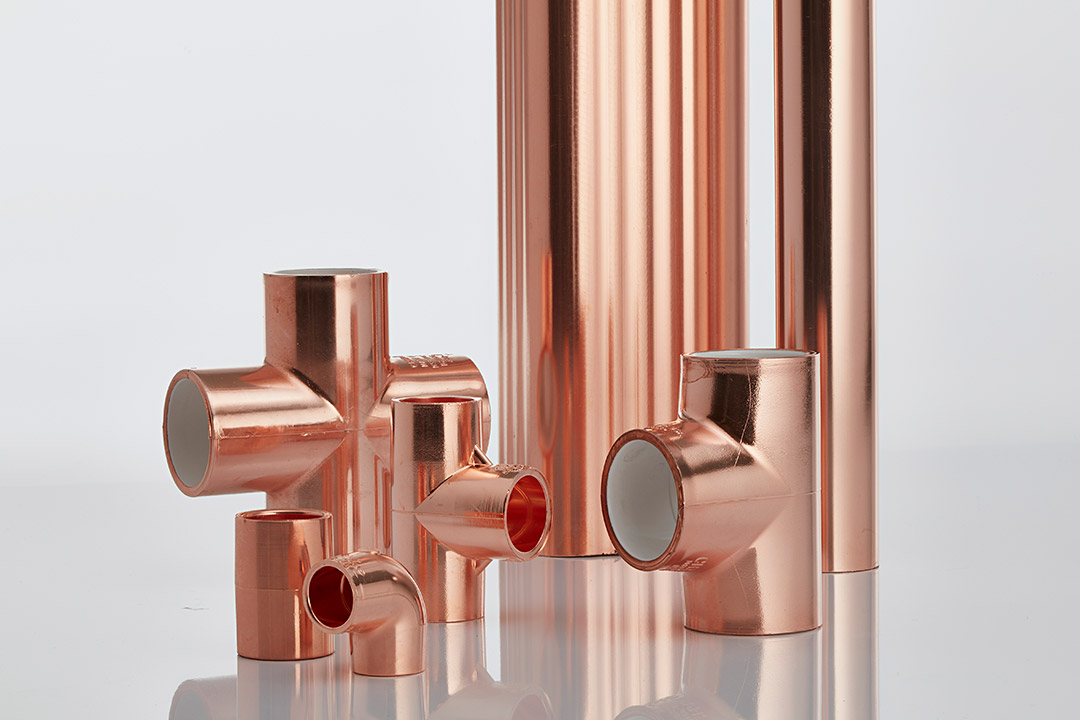
SAT’s Surface Activation® technology creates high adhesion platings that survive aggressive thermal cycling
Why Use PVC and CPVC?
PVC offers a dynamic array of modification options, which allows it to be used in a wide variety of different applications. This can range from piping where it is exposed to extreme heat, to catheters, where flexibility is required.
PVC is also a malleable material, which gives it a multitude of applications within the medical field. It is commonly used in bypass-sets for the heart of the lungs, blood giving or taking sets, and hemodialysis sets. This is due to a multitude of reasons, including the cost effectiveness of the material, the kink resistance, the softness of the material, and the sterilization capabilities.
A Closer look at PVC and CPVC
PVC—also known as polyvinyl chloride—and CPVC—also known as chlorinated polyvinyl chloride—are synthetic plastic polymers. They generally come in two different forms, those being rigid PVC and flexible PVC. Rigid PVC is generally used for pipes and doors, while flexible PVC is used for cable insulation and as a replacement material for rubber.
PVC is highly modifiable, which affords it the ability to be specialized depending on its application. For instance, flame retardants, UV stabilizers, and impact modifiers can be added to PVC to increase its usability in those respective fields.
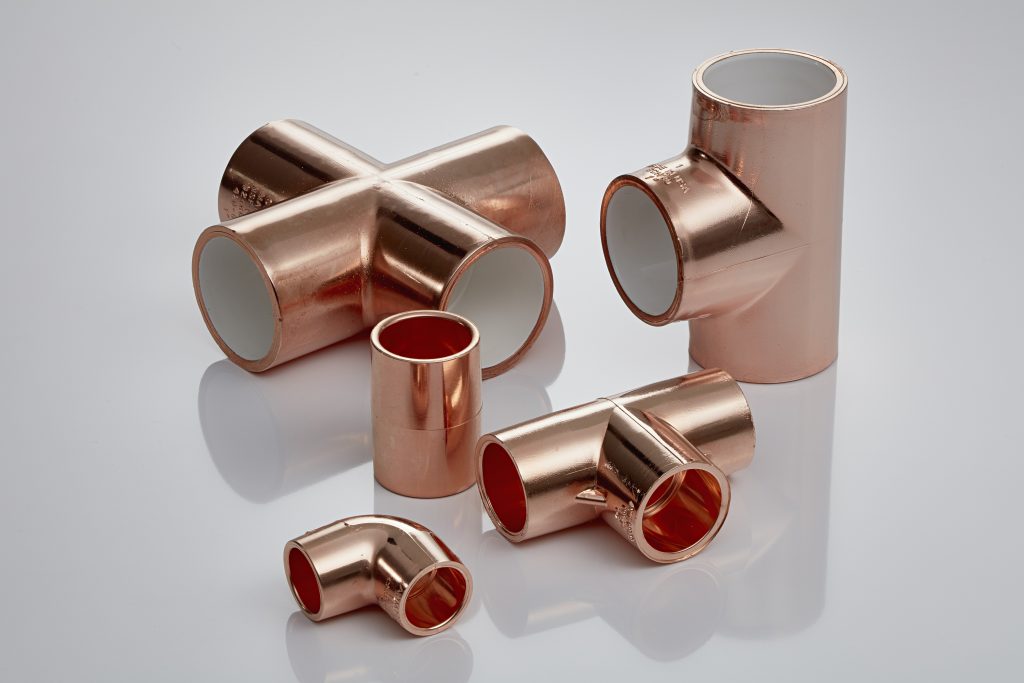
The natural heat stability for PVC is very low, offering a maximum operating temperature of 140 °F (60 °C) with a melting temperature of 212 °F (100 °C), but this is where the modification through polymerization is incredibly useful. Depending on what additive is used, the melting temperature can rise upwards to 500 °F (260 °C). This is bolstered by the materials natural insulation, which helps maintain temperature stability when exposed to hot or cold liquids.
Due to PVC’s insulation properties, the material offers high dielectric properties, dielectric loss tangent value, and volume sensitivity. These properties make PVC a good insulation material for medium to low frequencies.
PVC is also recyclable and sustainable. PVC can be recycled around seven times, which gives it a lifespan of nearly 140 years. This is especially important since the material is made with petroleum, which is a nonrenewable resource. This recycling process increases the use of PVC while also reducing petroleum output.
The major differences between PVC and CPVC are the materials melting point, malleability, and fire retardant properties. CPVC boasts a higher maximum operating point than PVC at 200 °F (93 °C). This allows CPVC more dynamic application within the realm of piping since it can withstand higher water temperatures. CPVC is also more malleable than PVC, affording it more applications due to its ability to be molded. Finally, CPVC is also naturally fire retardant, forgoing the need for additives.
Another notable difference between PVC and CPVC is that CPVC is an overall stronger material. It offers greater ductile strength than? PVC, as well as greater flexural and crush resistance, which allows it to be subjected to higher stress than PVC. These qualities have also afforded the CPVC the ability to replace metal piping in construction since it offers a natural corrosion resistance that metal simply cannot.