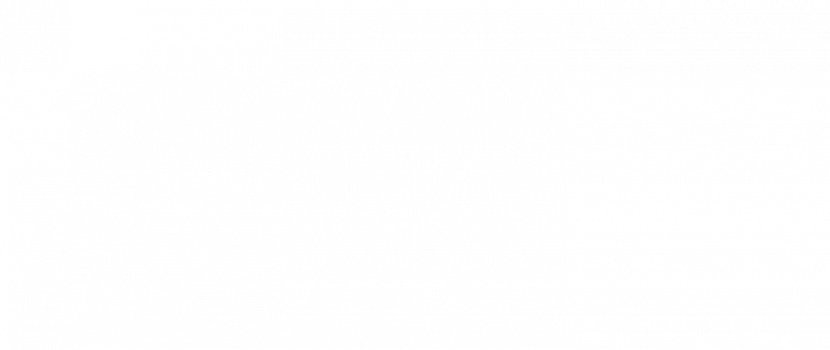
Due For A Product Redesign? Consider Injection Molded Parts with Plating
As industries across the globe strive for innovation and improvement, the question often arises: “Is it time for a redesign?” However, acknowledging that it’s time to redesign a product and actually taking the first steps are two different beasts, which is where injection molding comes in. Injection molding combined with plating is a marriage of cutting-edge technologies that opens up a world of possibilities for product redesign and product development. As consumer demands and expectations rise, staying ahead of the curve means exploring every avenue for improvement, and the combination of injection molding and electroplating delivers transformative changes that redefine what’s possible.
The Process of Plating on Plastic
The process of plating plastics is a meticulous and highly specialized technique that involves several crucial steps. First and foremost, it begins with thorough surface preparation. The plastic substrate undergoes a series of cleaning processes and surface treatments to ensure it is free from contaminants and ready to receive plating.
Once the surface is properly prepared, the next step involves applying a conductive “strike” layer to the plastic. This layer, often made of copper or nickel, serves as a foundation for the electroplating process. It enables the uniform deposition of the plating metal onto the plastic substrate.
With the conductive layer in place, the plastic component is immersed in an electroplating bath containing the metal plating ions, such as copper, nickel, tin, or gold, suspended in a solution. When an electric current is applied, the metal ions are attracted to the conductive layer on the plastic’s surface, resulting in a gradual accumulation of the plating material.
Throughout the electroplating process, precise control of factors like temperature, voltage, and plating time is crucial to achieve the desired thickness and quality of the plated layer. Quality control measures, such as regular monitoring and inspections, ensure that the plating adheres uniformly and flawlessly to the plastic substrate.
Benefits of Injection Molding
Injection molding offers numerous benefits when it comes to producing precisely manufactured plastic components. One of its standout advantages lies in cost-effectiveness and scalability, as it enables the production of complex shapes and intricate designs with minimal material waste. Moreover, injection molding provides unparalleled design flexibility, allowing for the creation of intricate geometries, undercuts, and thin-walled parts that would be challenging or impossible with other manufacturing methods.
Efficiency is another key strength, with rapid production cycles and consistent, high-quality output. In product redesign, injection molding can breathe new life into existing designs by reducing production costs and improving product performance through innovative shapes and materials. It’s a versatile and efficient approach that continually reshapes industries.
Benefits of Plating on Plastic
Electroplating on plastic parts brings a myriad of advantages to the table. Beyond the evident aesthetic enhancement, it significantly bolsters the durability and corrosion resistance of plastic components. Plating provides EMI shielding against environmental factors and outside electronic attacks, making it ideal for aerospace and defense systems. Plating plastics does more than enhance appearance; it combines the versatility of plastics with the durability, conductivity, and corrosion resistance of metals, extending the product’s life and enhancing its performance.
Different Types of Plating Metals and Their Uses
Understanding the different types of plating metals and their uses is crucial for making informed choices in various projects. Ultimately, the use case will dictate the type of metal deposited onto the plastic substrate, but there are a variety of options. Nickel and copper are valued for their protective qualities and electromagnetic isolation capabilities. Tin is a versatile metal that provides good corrosion resistance, ductility, and solderability. Gold, being a noble metal, will not corrode or oxidize and has excellent conductive properties as well as being highly aesthetic. These metals each bring unique properties to the table, allowing designers and engineers to tailor their choice to specific project requirements, whether it’s about aesthetics, durability, or functionality.
The Challenges of Plating onto Plastic
Plating onto plastic presents a set of distinct challenges that require careful consideration. Adhesion is a primary concern, as ensuring the plated layers adhere firmly to the plastic surface must be done with utmost care. Additionally, material compatibility between the plastic substrate and the plating metal must be thoroughly evaluated to prevent issues like peeling or delamination.
Adjacent to adhesion is surface preparation, which involves cleaning and conditioning the plastic, as it greatly influences the quality of the plated finish. To overcome these challenges, it’s vital to employ expert techniques, such as SAT Plating’s Surface ActivationⓇ and the use of specialized plating control systems. By addressing these considerations proactively, the potential of achieving high-quality and enduring plated plastic components becomes a reality.
Electroplating Applications
Electroplating can be used in a variety of different industries and applications with great effect.
Automotive Applications
In the automotive sector, electroplating plays a pivotal role in enhancing both aesthetics and durability. From chrome-plated trim that adds a touch of elegance to corrosion-resistant components, it elevates the overall appearance and longevity of vehicles.
Aerospace Applications
Aerospace demands the utmost in performance and reliability, making electroplating on plastic a valuable asset. Lightweight components with enhanced electrical conductivity, coupled with protection against extreme environmental conditions, make it indispensable in the aerospace industry.
Medical Applications
In the medical field, the advantages of electroplating on plastic are paramount. Biocompatible and sterilizable components ensure patient safety, while dependable performance in critical healthcare settings sets the standard for medical devices and equipment. Electroplating contributes to the precision and reliability required in the medical industry.
Final Thoughts
To stay ahead in today’s era of heightened demands on all products, , manufacturers must continue to explore every avenue for improvement. The combination of injection molding and electroplating unveils transformative possibilities that go beyond meeting standards; they set entirely new ones. Whether you’re envisioning producing connectors for aerospace applications or robust automotive components, this synergy promises a world where your products shine in every sense.
If you’re ready to embark on this journey, selecting the right plating material and component design, and plating partner is crucial. At SAT Plating, we offer comprehensive support spanning from R&D and prototyping, to large-scale manufacturing and seamless product delivery. Contact our knowledgeable team today to begin discussing your project’s specific needs and discover how SAT Plating can assist in meeting your exact specifications. Our capabilities extend to accommodating programs that require as few as 1,000 parts or exceed 1+ million parts annually. Welcome to a future where your product’s potential knows no bounds.