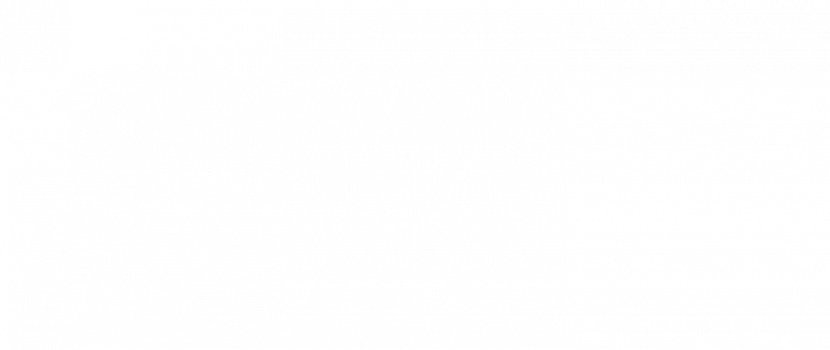
Lightweighting with Composite Connector Shells in Aerospace Applications
Lightweighting is critical in today’s aerospace design engineering. Since connectors and connector shells are integral to any aircraft, it’s worth looking at plated composite and polymer connectors for reducing overall weight.
Lightweighting with Innovative Plastics
Reducing the overall weight of an aircraft or any airborne product will increase energy efficiency and decrease fuel consumption. In one example, “for the Boeing 787, a 20% weight saving resulted in 10%–12% fuel efficiency improvement.” Lightweighting in aerospace also improves flight performance, leading to faster acceleration and obvious economic benefits.
Design engineers are challenged to either use less or lower-density material or both while maintaining the same or better technical specifications and performance in all aspects of the aircraft – from wing structures to communications systems. Many turn to engineered polymers and composites. Using these materials–like PEEK and Ultem–for housings and electrical connectors is cost-effective, while injection molding allows for high-volume manufacturing.
Connectors and housings can be made from polymers and composites that are electrically insulative, dimensionally stable, with high strength and low flammability. There are thousands of connectors on complex aircraft, so significant weight savings can be had when approaching the design of these connectors and connector housings with a focus on innovation.
Another bonus? Connectors and connector housings are typically the same or similar parts that can be used and manufactured in large numbers, so both the cost savings and lightweighting can be significant.
Aluminum and steel alloys are still the most prevalent materials in aerospace applications, though polymer and composite materials like PEEK, Ultem, and carbon fiber reinforced polymers (CFRP) are becoming more common.
Plating Polymer Connector Shells
Connector shells are critical interface points for most of the essential systems in an aircraft. The high performance and high-tech applications for these connectors make these parts vitally important.
Today’s aircraft are designed with multitudes of electronic and electrical systems–for flying, monitoring, and navigation; managing engine performance; communication during departure and landing; in-flight entertainment; and much more. Some of these systems require cabling that runs the length of the craft and can involve several hundred connections each. Connector shells protect from EMI signals and other types of interruptions, and they must maintain a “clean” flow for the data or power that goes through them.
EMI Shielding on Composite Connectors
While polymers are an excellent material for connectors in aerospace applications, the signals that ensure the proper functioning of a plane or spacecraft must be protected for both performance and safety. That’s one reason many design engineers choose metal-plated polymers, specifically copper and nickel plated onto PEEK and Ultem, for maximum performance that meets strict technical specifications.
These innovative connector housings are easily manufactured and plated in large quantities while offering a significant improvement on lightweighting efforts. Design engineers can rely on experienced experts in the injection molding and plating industries to meet their exacting specifications.
At SAT Plating, we provide high-performance plating solutions for some of the largest aerospace and defense manufacturers in the world. We can help your design and engineering teams determine the best approach for transitioning from aluminum or stainless steel connector housings to metal-plated PEEK or Ultem. While it may be a new approach for your organization, we’re here to help your team hit new lightweighting targets.