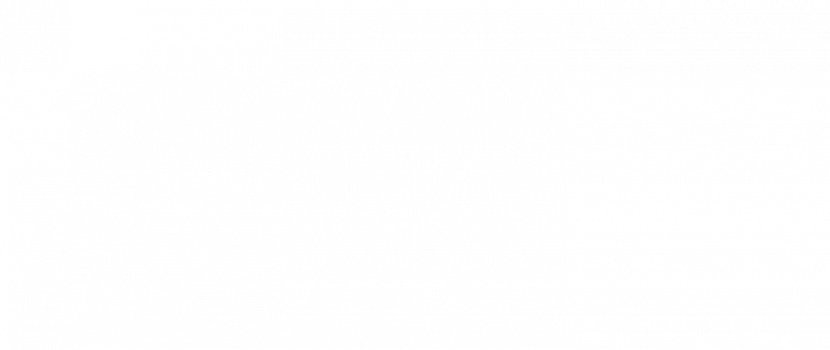
Five Reasons to Transition to Plated Polymers for Aerospace Connectors
Aerospace design engineers looking for a cost-effective, durable, and reliable option for lightweighting connectors and connector housings should consider transitioning from aluminum and steel alloys to plated polymer connectors.
Why Plated Polymers for Aerospace Connectors?
The aerospace connector industry has been through many transformations throughout history. From the early days of flight to today, there are always new challenges ahead for this group that make the cables and connectors that integrate aircraft systems. It’s no different now in an era where design engineers explore lightweighting and miniaturization options, while navigation and communication systems are more critical than ever before. Innovation is critical to success in aerospace engineering.
Strength-versus-weight considerations are ongoing, and plating on high-performance plastics offers a solid alternative to steel and aluminum alloys. In particular, plated PEEK®, Ultem® and carbon fiber reinforced polymers (CFRP) provide compelling reasons to switch from traditional stainless steel or aluminum connector shells.
#1 – Cost Reduction
Controlling aircraft design and operation costs is an increasing challenge for the commercial aerospace industry. Plated polymer connectors and assemblies consistently deliver performance and increasingly lighter-weight solutions for customer applications.
Design engineers achieve cost reductions when plating on plastics since injection-molded connectors can achieve economies of scale and are less costly to produce than those using traditional metal machining methods. The overall cost reduction with the transition to plated polymer connectors may not seem significant, but coupled with the lowered cost due to lightweighting and less fuel consumption, it becomes an important benefit over the lifetime of the aircraft.
#2 – Weight Reduction
How much weight reduction can you expect from a plated polymer connector shell? Polymer components weigh 20-30% less than comparable metal parts, directly impacting fuel efficiency. In one example, for the Boeing 787, it’s estimated that a 20% weight savings can provide a 10-12% improvement in fuel efficiency.
That weight reduction and the accompanying fuel efficiency contributes to a reduced carbon footprint and better overall aircraft performance.
#3 – Proven Performance
Plated polymer/composite connectors are certified and used in many commercial and defense products today. Innovative design engineers choose metal-plated polymers, specifically copper and nickel plated onto PEEK® and Ultem® injection-molded connectors, housings, and assemblies, for maximum performance that meets strict technical specifications.
On their own, advanced high-tech polymers have demonstrated qualities that design engineers seek for aerospace applications. For example, Ultem® resin provides temperature resistance well beyond 200°C, excellent dimensional stability, inherent flame retardancy, and low water absorption. Thin coatings of metal (plating) can add even more desired qualities, like EMI shielding and grounding.
A multi-pin electrical connector can be molded with carbon fiber-filled PEEK for enhanced strength and thermal stability in just one example. Copper and nickel plated to these connectors adds the necessary lightning strike and salt fog/corrosion protection.
#4 – Unique Combinations
Advanced polymers typically have half one-sixth of the density of steel and half the density of aluminum, and several varieties offer unique properties. Adding glass or carbon fiber adds stiffness with a high specific modulus. In addition, certain polymers provide high dielectric strength, so plating metal can add conductivity and grounding properties.
These polymers can withstand extreme temperature cycles and corrosion testing that may destroy metal connector assemblies, and they perform well during extended vibration and mating cycles.
With so many different polymers and metals available, design engineers have plenty of options for creating the best possible project-specific material combinations for connectors and assemblies.
#5 – Proven Supply Chain
While transitioning from aluminum and stainless steel connectors to plated polymers may seem like a complex and challenging process, several partnerships already exist between connector industry players and polymer vendors, injection molding companies, molding tool fabricators, and experienced plating companies like SAT Plating.
We provide engineered plating solutions for some of the largest aerospace and defense manufacturers around the globe. Contact us now so we can begin working with your design and engineering team to help make the transition from aluminum or stainless steel connector housings to metal-plated composites, such as PEEK® or Ultem®. It may be a new approach, but SAT Plating is here to help you hit your new aggressive lightweighting targets.