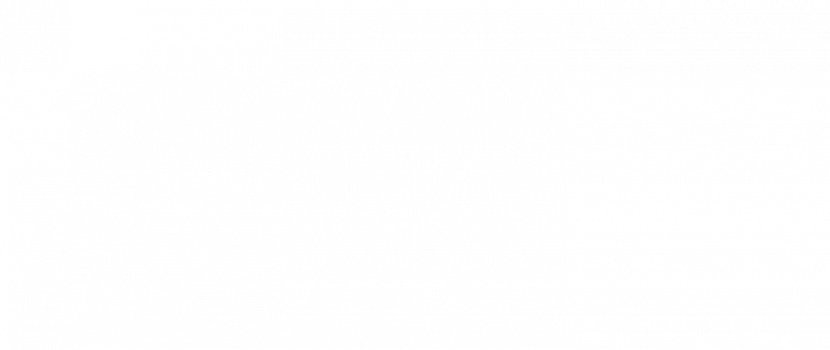
Thermoplastic Composites In Defense & Aerospace
Aerospace and defense engineers are paying increasing attention to thermoplastic composites as a cost-efficient option to replace metallic and thermoset composite parts.
What are thermoplastic composites?
According to Science Direct, “thermoplastics are a class of polymers that can be softened and melted by the application of heat, and can be processed either in the heat-softened state (e.g., by thermoforming) or in the liquid state (e.g., by extrusion and injection molding).”
Thermoplastics are pliable at certain higher temperatures and become solid when cooled. They offer increased impact resistance, lightweight properties, enhanced strength, unique processing capabilities, and even certain environmental advantages.
Thermoplastic composites, commonly referred to as TMCs, incorporate additional materials and serve as a natural evolution from structural polymer composites. A thermoplastic matrix ensures chemical stability. TMCs soften when heated and can be remolded into different structures without degrading or solidifying when cooled.
Thermoplastic composites are used as an alternative to thermosetting materials, or “thermosets,” wherein a chemical reaction of resin and a hardener or catalyst are combined, undergoing a chemical reaction to create a rigid, infusible product. Thermoset plastics cannot be re-extruded and are not easily recycled.
The value of thermoplastic composites in defense and aerospace
TMCs are known for high impact resistance, strength, lightweighting properties, and reduced environmental impact. This has the aerospace and defense industries using them to replace metal and thermoset composite parts.
Thermoplastic composites typically include 50-60% carbon fiber in aerospace and defense, creating specific mechanical properties and offering manufacturing flexibility. A more significant proportion of carbon fiber can help maximize mechanical performance, but it can make the material more suitable for longer cycle time manufacturing and higher pressures. Less carbon fiber is a better choice for faster cycles and lower pressure.
The increasing use of automation in manufacturing environments makes a strong case for thermoplastics over thermosets. The use of thermoplastic composites in defense and aerospace brings cost savings, durability, and invaluable lightweighting qualities. For example, reducing the weight of an aircraft or piece of machinery increases fuel efficiency, while the reusability of thermoplastics adds to the eco-friendly factor.
Design engineers are using thermoplastic composites to:
- Reduce manufacturing cycle time
- Decrease weight of structures and aircraft by up to 50% vs. metal solutions and up to 20% vs. thermosets
- Increase sustainability – lowering emissions with a recyclable material
Let’s talk about Plating Thermoplastic Composites
While thermoplastic composites offer customizable qualities, adding a plated metal surface to a thermoplastic piece can add EMI Shielding, conductivity, and grounding properties. With so many different polymers, combinations, and metals available – each with unique properties – design engineers have incredible options for creating innovative project-specific material combinations for their aerospace and defense programs.
At SAT Plating, we support design engineers from some of the world’s largest aerospace and defense manufacturers. Get in touch with us, talk to a plating specialist, and let’s work together to help your design and engineering team take advantage of today’s most innovative materials and plating options.