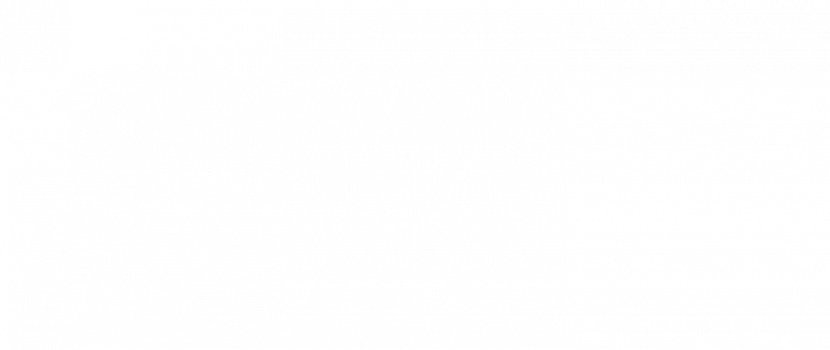
Examining Connector Specifications in Aerospace and Military Applications
Connector specifications are becoming more stringent in aerospace and military applications and rightfully so. Operating aircraft at hundreds of knots per hour at tens of thousands of feet above the earth requires strict standards that virtually eliminate the possibility of failures. Issues like electromagnetic interference, heat, and vibration must be mitigated all while using lightweight yet durable materials for the interconnect system. One of the best options for delivering a durable connector that meets light-weighting goals is with electroplating high performance plastics. When done in conjunction with military specifications, this method can be ideal for A&D manufacturers.
Performance Requirements for Military and Aerospace Connectors
In order for a connector to be MIL-SPEC, it must follow the stringent guidelines set forth by the US military. These types of performance requirements mostly have to do with thermal stability, vibration resistance, lightning-strike survivability, corrosion resistance, and general durability.
Connectors must be able to withstand extreme temperatures that can be encountered in different operating environments. The range of these temperatures usually falls between -65°C and +175°C, although some specialized connectors may be required to perform in even more extreme temperature ranges.
Vibration resistance is also crucial for connectors given the constant motion in any aircraft. Takeoff, landing, and high speed maneuvers can cause significant stress on different components. Therefore connectors must meet stringent standards such as MIL-STD-1344 or specific RTCA/DO-160 requirements.
Aircraft are also exposed to different environmental conditions such as ocean water spray, humidity, moisture, and a litany of chemicals used to maintain aircraft. MIL-STD-202 evaluates a material’s ability to resist corrosion.
Connectors must also be tested for lightning strike resistance to ensure their reliability and safety during operation. Lightning strikes can generate intense electromagnetic fields and cause significant electrical surges, which can potentially damage or destroy sensitive electronic components. To test connectors for lightning strike resistance, a series of standards have been established to evaluate the connector’s ability to withstand direct and indirect lightning effects. These include high voltage transients, high current surges, and induced electromagnetic fields.
Last of all, connectors must be generally suited to withstand the stress of high speeds, dust, fumes, water/moisture, humidity, low air pressure, extreme temperatures, and abrasions. Robust material selection is necessary to ensure that these connectors are resilient enough to handle the demands of flight.
Manufacturing Considerations for Military and Aerospace Connectors
When considering manufacturing military and aerospace connectors, there are essentially two characteristics that must be prioritized: Durability and weight. The best way to maximize the durability of a connector while keeping the weight as light as possible is with the use of alloys and composite materials. One of the best ways to achieve this is by plating injection molded high-performance plastics. Manufacturing connectors this way ensures highly accurate contact design and the ability to customize any connector per specifications.
The Role of Electroplating in Connector Manufacturing
Electroplating is the unsung hero that enables light-weighting with high-performance plastics. Well known composites include PEEK and Ultem. Electroplating is a process that covers a connector with a surface layer of conductive material such as Copper and Nickel. This creates the best of both worlds where weight is reduced through the use of plastic, but the durability, conductivity, and overall functionality of metal is maintained. SAT Plating uses their proprietary Surface ActivationⓇ and other pre-plating treatments to electroplate composite connectors for superior performance and lighter weights.
Ensuring Quality and Reliability in Connector Manufacturing
Finally, quality control within connector manufacturing and electroplating is critical to maintaining consistent performance when conducting high-volume production. Not only does the injection molding and electroplating process need quality control, but design also needs a careful eye to ensure efficiencies and a high-quality end product. Partners like SAT Plating are qualified and able to oversee quality assurance of the entire electroplating process. We have the experience to advise and consult on the best options for your unique product and see the project through to completion, on time and on budget.
Conclusion
Aerospace and military connector specifications are necessary for ensuring maximum safety and high performance within the A&D industry. A&D manufacturers need partners who understand the importance of light-weighting while still maintaining MIL-SPEC standards. SAT Plating can help A&D companies with everything from R&D to high-volume manufacturing and shipping the finished product. Get in touch with our experts today to discuss your project’s requirements and how SAT can help meet specifications. We support programs with volumes as low as 1,000 parts to well over 1 million parts per year.