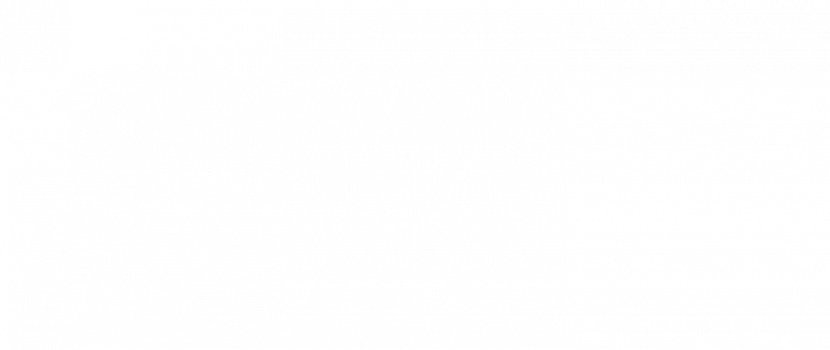
The Importance of EMI Shielding in Electric Vehicles
In an automotive industry that’s bullish on electric vehicles, electromagnetic interference (EMI) shielding is becoming even more critical to manufacturers and their tier one and tier two suppliers.
Electric Vehicle (EV) manufacturing inevitably requires installing electronic systems into a confined spaces and somehow keeping the electromagnetic energy generated from these systems from “crosstalking” and causing malfunctions and failures.
Developing an EMI-protective enclosure around the EV connectors, cables, and components can help automotive design engineers reduce EMI between systems and avoid significant performance and reliability issues.
Sources of EMI in Electric Vehicles
Electric vehicles are engineered with extensive sensing equipment to allow for innovations in self-driving, efficient traffic management, and high-tech safety features. This sensitive equipment uses radio and other signal-based communications devices that benefit from EMI shielding.
Shielding can also help prevent damage to and malfunction of electrical and electronic components from corrosion, heat, and other challenging conditions.
While EMI can cause basic nuisance concerns like static on the radio; it can also lead to much more significant problems like issues maintaining control over the vehicle. Systems that contribute to safety and performance are typically priorities when it comes to EMI shielding.
Some of the primary sources of EMI from inside an electric vehicle include:
- Power converters and electric motors
- Traction batteries and interconnectors
- Shielded and unshielded cables
- Battery chargers
- Collision avoidance radar
- DC motors
- Engine control modules (ECM)
- Navigation systems
Plastic for EMI Shielding
Shielding agents are one of the most common methods for preventing EMI. There are a variety of options when it comes to this protection.
One type of EMI shielding can be applied using acrylic-based sprays or brush-on coatings that add shielding properties; other types of shielding require creating EMI-resistant enclosures around sensitive electronics. Yet another option is applying shielding materials to plastic enclosures that surround the sensitive electronic devices or components.
Innovative plastics like PEEK, Ultem, and other high-performance polymers allow custom enclosures to be 3D-printed to exacting standards from design and electrical engineering teams. These polymers can help overcome EMI, highly corrosive environments, and extreme heat in electric vehicles, buses, trains, and other forms of transportation.
Plated Polymers For EMI Shielding
EMI shielding using plastics plated with metals is an effective option because metal adds the ability to reflect back some types of interference.
Copper, silver, nickel, or a combination of these metals are frequently plated onto advanced polymers for added shielding and protection. The amount of EMI shielding that’s created is dependent on the materials and thickness of the application.
Looking Toward Future Mobility
Automotive manufacturers are in the development of new and exciting options for future mobility. With GPS, RADAR, LiDAR, and RF systems, future vehicles will essentially become transmitters and receivers. The accompanying signal interference issues have led to our OEMs becoming even more appreciative of the incredible value of EMI shielding.