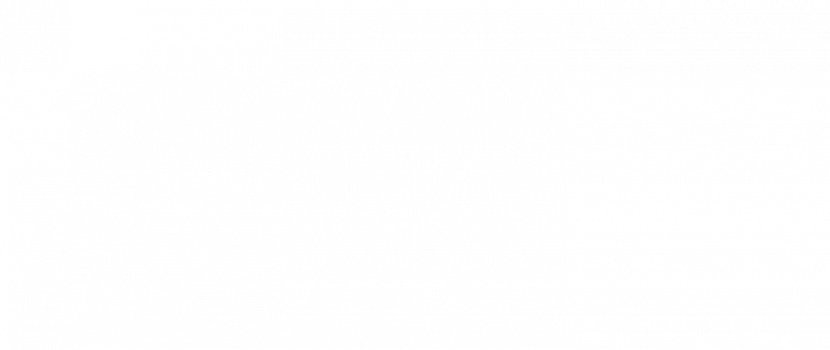
The Future of Nickel Plating
Nickel plating is one of the most versatile plating options available and its popularity is likely to continue to grow in the aerospace and defense industries. The evolving needs of engineering teams in the fields will likely continue to drive ongoing advancements in the nickel plating industry.
What is Nickel Plating?
A coating of nickel or a nickel alloy can be applied to just about any existing surface – typically a product or part – with traditional electroplating processes using an electric current and electroless processes which occur through autocatalytic reaction.
Plating with nickel can be done in several ways. With a metal substrate, technicians use either the chemical or electric method, dispersing a thin layer of nickel or a nickel alloy coating. In electroplating, a slight current is passed into the substrate, causing an oxidation process that disperses the metal flakes and salts to create an evenly-layered coating on the item being plated. The electroless process does not use a current but makes use of a chemical reaction to create similarly, and sometimes more stable, results on metal, polymers, and composite objects.
The History
Plating has been in use throughout the last few hundred years for both aesthetic and functional reasons. In the early 1800s, the development of electrochemical piles, basically the first electrical battery, meant that inventors and technicians could now pump a current through wires.
In 1837, Golding Bird, a British physician who researched the use of electricity and electrochemistry in medicine, described the first examples of electrodeposition of nickel chloride or sulfate on platinum. His team was able to apply a thin coating of nickel on a platinum substrate. Soon afterward other European experiments demonstrated that nickel chloride, nitrate, and nickel ammonium sulfate could also be used for nickel plating processes. The nickel ammonium sulfate solution, also known as double nickel salts, was the industry standard for the following seventy years.
Dr. Isaac Adams is known as “the father of nickel plating” in the United States, after patenting a nickel ammonium sulfate bath in 1869. Other researchers joined in and in 1916, O.P. Watts developed a rapid nickel plating bath that’s still used around the globe today. The basic “Watts Formula” is:
- Nickel sulfate, NiSO4 • 7H2O, 240g/l
- Nickel chloride, NiCl2 • 6H2O, 20g/l
- Boric acid, H3BO3, 20g/l
Plating companies used a variety of temperature and air agitation levels in both the United States and in the United Kingdom until international standards were created and promoted in the 1930s. These standards included higher bath temperatures and increased air agitation.
The Watts formula has evolved as new capabilities were introduced, like the varied compositions required to create “bright” (shiny) nickel plating. Chemical composition was also introduced to allow electroless nickel plating. The fact that they don’t require a steady source of power means it’s sometimes more cost-effective. Both electric and electroless nickel plating is used around the world in a wide range of industrial and consumer applications.
The primary reasons behind nickel plating include:
- Strengthen metals against rust and other forms of corrosion
- Protect lightweight plastics from wear and tear
- Add aesthetic value to a dull appearance
- Increase the hardness of the underlying surface
- Add resistant for alkaline environments
- RFI/EMI shielding
The Future of Nickel Plating for the Aerospace and Defense Industries
The future of nickel plating in the aerospace and defense industries looks bright. Engineers can rely on this to fend off the atmospheric corrosion of extreme conditions, which causes damage that can penetrate aircraft and other machinery, weakening them structurally. A zinc-nickel coating is extremely effective in this application, as it acts as a “sacrificial coating,” absorbing the corrosion before it gets to the substrate.
Additional uses include:
- Increasing hardness – Aircraft and defense equipment are operated under the most extreme conditions, so nickel electroplating parts reduces wear and tear and increases longevity.
- Refurbishing parts – When a part gets worn, a nickel coating can help restore the part or component to its original dimensions, inside or outside.
- Adding electrical conductivity to parts and elements made of durable polymers
- Adding resistance for highly acidic or alkaline environments
- Increasing lubricity and resistance to chemicals on engine parts, mounts, compressor blades, and other flight-critical components
What Does the Future Look Like?
It is likely that this industry will continue to grow, as this plating technique’s versatility continues to serve the needs of engineers around the globe. The aerospace and defense industries will continue to exploit the full potential of nickel plating in engineering and electroforming applications while plating companies like SAT Plating will continue to evolve their services to meet the unique needs of the market.
SAT Plating Is A Leader In Nickel Plating
SAT Plating is a leader in nickel plating, developing technical solutions for applying metal platings to high performance engineered polymers. We deliver controlled and repeatable technical solutions, aiming to improve every day, with every product we make. We aim to reduce and identify risk, surpass the requirements for any and all requested products, meet or exceed your expectations; and work together as a happy and efficient team.
Learn more about us: https://www.satplating.com/about-us/