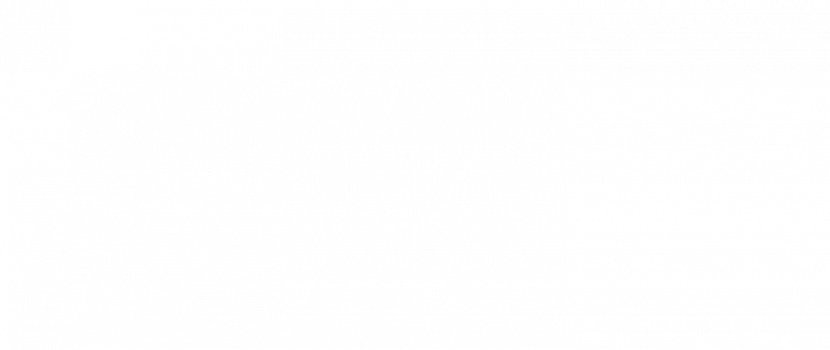
Plating 3D Printed Parts – Challenges & Considerations
Whether called 3D printing, rapid manufacturing, or additive manufacturing, this industry is experiencing explosive technical growth. With each passing year customers have an ever-increasing choice of manufacturing techniques and machinery, but also an equally expanding selection of polymer choices with improved performance characteristics.
SAT Plating is keeping abreast with this changing landscape by participating and exhibiting at the RAPID + TCT show each year. There we are able to stay current with the latest materials and machines – resulting in our ability to develop a range of solutions for metalizing plastic AM parts.
Following are some of the observed challenges and considerations to metalizing these parts and plastics:
3D Printing Techniques & Material Selection
SLA, PolyJet, etc.
These techniques generally utilize a UV curable working liquid. Before plating, this type of part requires post-treatments to rinse off uncured chemistry, plus a thermal bake to ensure full polymerization of the acrylic monomer. The post-bake also locks in the final dimensions of the part. Parts made with these techniques can be relatively smooth with fine details.
FDM, SLS
These techniques work by melting filaments or powders of different polymers. The advantage is that these methods can use a broad array of commonly used plastics such as ABS, PA, PEI, PEEK. Generally, no post-cleaning or baking is required. Surface roughness and porosity depends substantially on manufacturing speed and resolution.
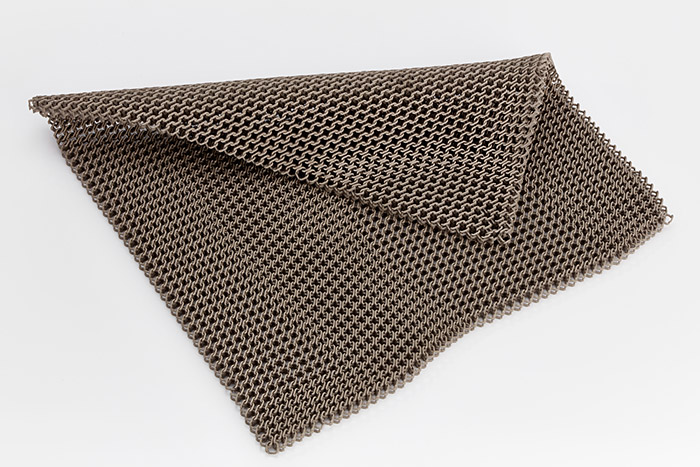
SLA with Satin Nickel Metallization
Metal Finishes & Benefits
Metal finishing of 3D parts has many benefits beyond appearance purposes. Functional features can include: UV protection, abrasion resistance, permeation barrier, RFI/EMI protection, conductivity, antennas, inductive charging circuits, microwave wave guides, and more. SAT Plating successfully applies metals to plateable rapid polymers, such as:
Chromes | Coppers | Nickels | Golds | Silvers
3D Part Roughness, Porosity, and Layering
Rapid parts are not nearly as smooth as injection-molded parts. Depending on the printing method and resolution of the printer, parts can be very rough and have heavy porosity. This roughness prevents the plating of smooth mirror-like finishes and porosity can create technical problems with plating chemistry retention – potentially causing latent plating discoloration or adhesion failure. The same can happen with parts whose walls were created via multiple layers of polymer, particularly with the SLA method. In some cases, plating chemicals migrate between the layers causing de-lamination or latent plating discoloration and failure.
Post-print Processing
Many companies are working on post-processing methods for smoothing rapid part topography – some involving heat, some solvents, some media tumbling. In all cases the surface topography does improve, but remains far short of the smoothness of an injection molded part.
3D producers also have the option of applying and hand-sanding multiple layers of a filler coating to improve the part finish. It is important to point out, when parts have this post treatment the plater is now trying to get the metal to adhere to the filler, not the base polymer. Some fillers are too soft or chemically incompatible to be plated.
SAT Plating has successfully plated many 3D printed products – our goal is to engage companies in the early stages of product design and development in order to help them with polymer selection and plating engineering. SAT will once again exhibit at the RAPID + TCT show next year in Detroit from May 20-23, 2019.